Deckel FP1 Fräsmaschine - (M)ein Bastlertraum
- Teil 2 -
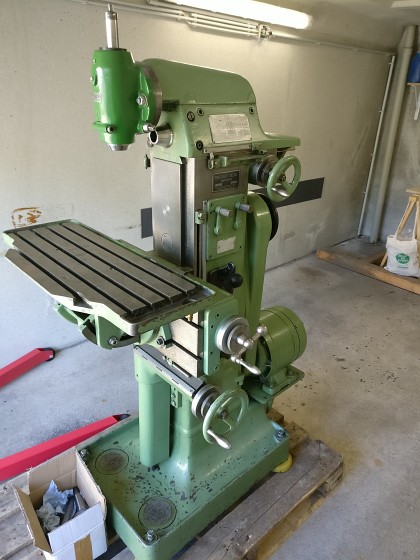
Bild 4 - Die FP1 ist in meiner Garage angekommen
Und jetzt?
So nun steht also eine fast 80 Jahre alte Fräsmaschine in meiner Garage!
Hier soll/kann sie freilich nicht bleiben, die Garage ist unbeheizt und verfügt nicht über Drehstrom.
Der Plan: In der Garage will ich sie in handliche (naja, die Einzelteile wiegen zwischen 30 und 200kg)
Teile zerlegen und gründlich reinigen. Dann will ich sie in meine Kellerwerkstatt bringen und dort wieder aufbauen.
Mein Ziel ist es nicht die Maschine bis zum "Neuzustand" zu restaurieren - dazu fehlen mit die Fähigkeiten
und Möglichkeiten aber auch die Motivation. Sie soll "nur" einmal gründlich gereinigt, geschmiert und justiert werden, so
dass ich sie die nächsten Jahre guten Gewissens nutzen kann, ohne jeden Augenblick mit einem Totalausfall
rechnen zu müssen. Das eine oder andere Ersatzteil wird wohl fällig sein, nach so vielen Jahren kein Wunder.
Die Elektrik ist zwar nicht mehr auf dem Stand von 1941 aber dennoch völlig marode. Die wird also
komplett erneuert.
Dass eine so alte Maschine eine gewisse Patina in Form von Kratzern und Lackabplatzern hat finde ich völlig OK und auch passend.
Von einer Neulackierung habe ich nichts und ein Ausstellungsstück, das man nur mit Handschuhen anfassen
darf brauche ich nicht.
Auf den Fotos und auch auf den ersten Blick sieht die Maschine tiptop ordentlich und sauber aus.
Bei genauerem hinsehen hat sich aber Öl und Schmutz über die Jahrzehnte hinweg an allen nicht ganz leicht zugänglichen
Stellen angesammelt. Allein im Fuß der Maschine, der eigentlich als Sammelbehälter für Kühlmittel dient, müffeln etwa 10 Kilo
von einem zähen Gemisch aus Öl, Fett und Spänen vor sich hin. Aber das war so zu erwarten und das habe ich auch bei der Besichtigung schon gesehen.
Soweit alles OK. Dass der Verkäufer den Vertikalkopf in einer Nacht-und-Nebelaktion vor meiner Besichtigung noch
schnell mit irgendeinem Flaschengrün überlackiert hat, um eine tiefe Scharte im Lack verschwinden zu lassen finde
ich schade, weil es so gar nicht zum Rest passt, aber das ist für mich kein Beinbruch und war für mich auch
kein Grund die Maschine nicht zu kaufen.
Die grüne Lackierung (es dürfte sich um Resedagrün, die "Standardfarbe" von Werkzeugmaschinen der '70er und '80er Jahre
handeln) ist übrigens auch schon nicht Original. Die Originalfarbe war Blaugrau, das war bis in die '60er Standard.
Immerhin sind die Neulackierungen einigermaßen ordentlich ausgeführt, so dass nicht gleich alles unkontrolliert abblättert.
Vorbereitung ist die halbe Miete
Dass ich mir da einen ca. 700kg schweren Gußklotz ins Haus holen werde war mir freilich vorher bewußt.
Ich habe mir schon vor dem Kauf viele Gedanken gemacht, wie ich die Maschine in den Keller bringe, ohne
das Haus, die Maschine oder gar mich selbst zu beschädigen....
Das Problem mit der Einbringung einer FP1 (oder anderer Maschinen diesen Kalibers) in einen Kellerraum hatten freilich schon
viele vor mir und so gibt es im Netz etliche nützliche Tipps und Erfahrungsberichte.
Manche haben eine betonierte (gerade) Außentreppe und können die Maschine mit einem Kettenzug auf Brettern hinabgleiten lassen.
Einen solchen Luxus habe ich leider nicht. Andere schnallen den Rumpf der Maschine auf eine Sackkarre und hoppeln
so Stufe für Stufe mit 3-4 Mann die ziehen und schieben hinab. Letzteres wäre mir zu ristank, denn der Schwerpunkt ist recht
weit vorn und wenn das Blatt der Karre abknickt, haben die unten stehenden Helfer ganz schlechte Karten.
Abgesehen davon wollte ich auch den Freundeskreis nicht schon wieder (...die Drehmaschine war vor einem halben Jahr dran)
mit einer solch bandscheibenaufreibenden Aktion belasten.
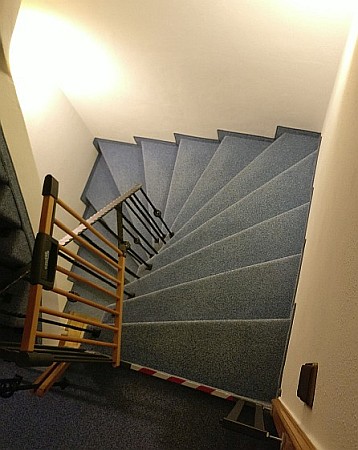
Bild 5 - Die Treppe in den Keller - keine einzige gerade Stufe und Teppichboden: Nix gut :-)
In meinem Fall ist es eine mit Teppichboden belegte U-förmige Kellertreppe, die mir Sorgen bereitet hat.
Die ist nicht gerade die Idealvoraussetzung für die Einbringung einer solchen Maschine. Aber immerhin gibts in meiner
Werkstatt ein großes Fenster mit Kellerschacht und direkt darüber ist ein dicker Dachbalken. Da geht doch was!
Das Motto lautete also: Zerlege die Maschine in möglichst viele gut handhabbare Einzelteile
Im Netz findet man Infos zum Gewicht der Einzelteile einer FP1. Somit wusste ich schon ungefähr womit ich es zu tun bekomme:
Tisch, Motor, Motorträger, Riemenverkleidung, Vertikalkopf mit Halter, Horizontalkopf und Z-Support sind Teile die sich relativ
einfach abbauen lassen und jeweils zwischen 15kg und 55kg haben. Allein ist das teilweise schon sehr grenzwertig, mit technischen
Helferlein geht es aber und zu Zweit ist es eh kein Thema.
Eine andere Kategorie sind aber die Maschinensäule und der Fuß: Zusammen ca. 350kg. Man kann die beiden Teile leicht trennen,
aber auch 150 bzw. 200kg am Stück sind Teile, bei denen man ohne technische Hilfen kapitulieren muss.
Man darf und kann das (leider) nicht mit einem schweren Schrank bei einem Umzug vergleichen, den man auch als ungeübter gerade
noch so zu zweit eine Treppe runter bugsiert. Diese beiden Teile der Maschine wiegen mindestens das doppelte eines Schranks,
sind schwer zu fassen und werden im Falle dass etwas "auskommt" schnell zu einem gefährlichen Geschoß, das man nicht mal
eben mit dem Knie an der nächsten Stufe abbremst.
In meinem Fall war also der Kellerschacht die Rettung für das Projekt Industriefräsmaschine!
Mit die wichtigste Vorarbeit: Geeignete Hebewerkzeuge besorgen, damit die Einbringung der richtig schweren Teile schnell
und sicher vonstatten gehen kann.
Werkstattkran
Vorab habe ich mir einen mobilen Motorkran besorgt, um in der Garage die mittelschweren Teile der Maschine auch allein
(..nachts, wenn man für solche Basteleien eben Zeit hat) abbauen zu können.
Die Standardausführung hebt 2 Tonnen Last. Ich habe mich aber für einen Kran mit nur 500kg entschieden,
denn der ist kleiner und leichter. Den hätte ich dann zur Not auch im Keller für den Wiederaufbau der Fräse aufbauen können.
Da ich nie vorhatte damit die komplette Maschine am Stück zu heben, war die geringere Belastbarkeit für meine Anwendung nicht
hinderlich.
Der Kran hat sich als absolut essentiell erwiesen, ohne hätte ich die Maschine nicht "klein" gekriegt. Ich musste ihn allerdings etwas modifizieren.
Diese Kräne sind dafür ausgelegt, dass man mit den vorderen Beinen unter den Motorraum eines KFZ fahren kann, um dann die
Last nah am Hebezylinder anzuheben.
Steht die Last dagegen auf dem Boden oder wie in meinem Fall auf einer Europalette, kommt man mit so einem Kran gar nicht
bis an die zu hebenden Teile ran, weil die V-förmig angeordneten Beine des Krans immer irgendwo anstoßen, weit bevor
man mit dem Ausleger ausreichend nah ran kommt.
Die passende (allerdings sehr viel teurere) Alternative nennt sich Palettenkran: Der sieht im Grunde genauso aus, nur sind die "Beine" parallel und
in gut 80cm Abstand, so dass die Beine außerhalb der Palette bleiben. So einer war mir zu sperrig und auch zu teuer.
Als ersten Schritt habe ich die vorderen beiden Rollen durch kleinere mit nur 45mm Durchmesser ersetzt, so dass einer der beiden
Füße unter die Palette reinfahren kann. Das hat schon viel gebracht.
Für manche Teile kam ich aber noch immer nicht nah genug ran, der Ausleger war auch ganz ausgefahren noch viel zu kurz.
Jetzt darf man den Ausleger freilich nicht nach belieben verlängern. Einerseits weil es den Schwerpunkt zu weit nach vorne
versetzt und der ganze Kran kippen kann und andererseits, weil durch den längeren Hebelarm die Konstruktion
schnell an ihre Grenzen kommt.
Für meinen Kran habe ich ein verzinktes Vierkantrohr mit 1m Länge besorgt und es so gebohrt, dass der Ausleger vorn bis zu 30cm
weiter reicht als das Original und hinten 10cm mehr zur Abstützung beim Hubzylinder hat. Die auf dem Kran
aufgedruckten Belastungswerte sind mit diesem längeren Ausleger freilich nicht mehr gültig und man muss bei jeder Last
mit gesundem Menschenverstand prüfen, ob die Konstruktion sicher steht und nicht überlastet wird.
Da das schwerste Anbauteil der FP1 gerade mal 55kg wiegt und der Kran selber gut 40kg auf die Waage bringt, bestand zu keinem
Zeitpunkt die Gefahr, dass er kippt oder überlastet wird, selbst wenn die Last mal ein paar Zentimeter vor den
vorderen Rollen war.
Noch eine Anmerkung: Zur Montage des Krans lagen bei meinem Schrauben gemischt mit 4.6 und 8.8 Festigkeit bei.
Anhand der Anleitung war nicht vorgegeben welche Schrauben wo hinsollen, das hat sich über die erforderlichen Längen
von selbst ergeben.
Dummerweise war es aber gerade so , dass an den heiklen Stellen (am Fuß des Zylinders, am hinteren Gelenk des Auslegers
und am Zugband hinten) nur die "schwächeren" Schrauben gepasst haben. Da mir das zweifelhaft erschien, habe ich
kurzerhand die "fehlenden" 8.8er Schrauben nachgekauft. Rechnerisch wäre es nicht nötig gewesen - aber sicher ist sicher,
und so eine Hand voll M12 Schrauben kostet nicht die Welt.
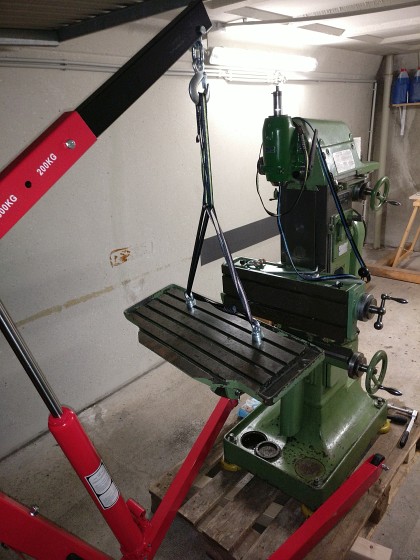
Bild 6 - In Originalausführung war der Kran keine große Hilfe: Der Ausleger war schon in der äußersten Position und
die Füße des Krans passten nicht unter die Palette und dennoch fehlten noch 30cm.
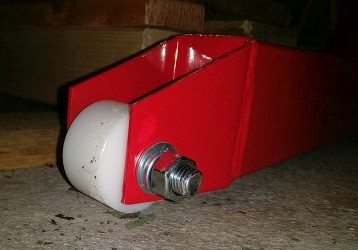
Bild 7 & 8 - Der Kran mit langem Ausleger und kleinen Rollen - Vor Nachahmung bitte Sicherheitshinweise im Text oben beachten!
Eine Alternative wäre es gewesen, die hinteren beiden Bohrungen für die Fußstreben weiter nach außen zu verlegen. Dadurch
kommen die Beine vorne weiter zusammen, so dass dann beide unter die Palette passen. Daran hat mich aber gestört, dass
der Kran dann leichter zur Seite kippen kann. Das war mir zu riskant!
Elektrische Seilwinde über dem Kellerschacht
Zum herablassen der schwersten Maschinenteile (Säule und Fuß) habe ich eine Seilwinde mit Elektromotor mit 300kg/600kg
(Güde GSZ300/600) verwendet.
Diese Winde kann (nach Herstellerangabe) direkt 300kg heben, über eine mitgelieferte Umlenkrolle schafft sie (bei halbierter
Hubhöhe und halbierter Hubgeschwindigkeit) 600kg.
Um die Winde oberhalb des Kellerschachts anzubringen, habe ich mir ein Vierkantrohr 45x45mm mit 4mm Wandstärke besorgt.
Wandseitig wird dieses Rohr von einen passenden Balkenschuh (Typ B) abgestützt. Diesen habe ich mit vier Schrauben (12x160mm)
in der (ungedämmten!) Ziegelwand festgedübelt. Am anderen Ende liegt das Rohr auf einem parallel zur Wand verlaufenden Dachbalken
(ca.150x200mm) auf. Die Höhe zur waagerechten Ausrichtung der Winde habe ich mit ein paar Gummipuffern unter dem Rohr eingestellt.
Die Tragfähigkeit dieser Konstruktion habe ich nicht berechnet, aber Gefühl und Erfahrung sagen mir, dass das
ein Mehrfaches der maximalen Last des Seilzugs trägt.
Recht ungünstig ist die Tatsache, dass sich die Steuertaster an einem nur ca. 1,5m langen Kabel befinden, die Winde musste
ich aber auf fast 3m Höhe montieren. Wenn ich die Teile im Keller "in Empfang nehmen" will, bräuchte ich also zwingend
eine zweite Person die die Winde bedient. Die Verzögerung in der Kommunikation ("HAAAALT!" "Hä? Hast Du was gesagt?
Die Seilwinde ist so laut!") und das ruckartige Verhalten des Motos waren mir zu unsicher, also habe ich das kurze
Steuerkabel gegen ein 6m langes ausgetauscht. Damit konnte ich die Winde auch vom Keller aus bequem bedienen und die
Last jederzeit beobachten und damit zentimetergenau positionieren.
Da das Seil nicht rostfrei ist, habe ich die Seilwinde nach erfolgreicher Einbringung wieder abgebaut, das (lackierte)
Rohr dagege bleibt.
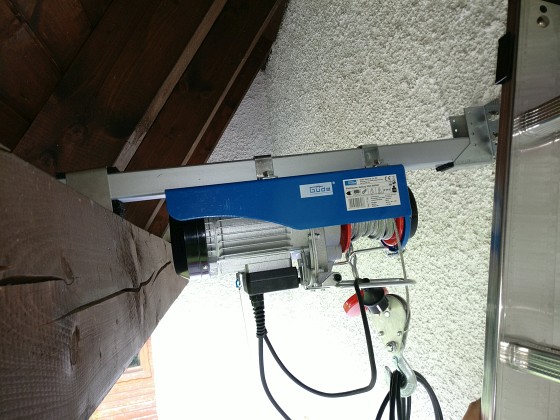
Bild 9 - Seilzug zwischen Hauswand und Dachbalken oberhalb des Kellerschachts
Kranbahn über dem künftigen Standort der Maschine
Da in den nächsten Jahren sicher immer mal wieder Teile der Maschine an-, ab-, und umgebaut werden müssen und mein
Rücken nicht jünger und leistungsfähiger wird, habe ich mich entschlossen eine 2m lange Kranbahn an der Decke direkt über der FP1
zu installieren.
Nachdem bohren in Stahlbeton furchtbar staubt und die Kranbahn schon bei der Einbringung behilflich sein sollte, habe ich
auch diese schon vorab angebracht.
"Echte" Kranbahnen mit "richtigen" Laufkatzen (z.B. Demag oder Abus) sind die sicherste Lösung und offiziell für die
spezifizierte Last zugelassen, sie sind aber für den Privatgebrauch unerschwinglich und - in meinem Fall entscheidend - sie
bauen sehr hoch. Bei nur 222cm Deckenhöhe in meiner Kellerwerkstatt war so was selbst für die recht niedrige FP1 keine Option.
Bei der Suche nach einer Alternative bin ich auf Laufschienen für Hallentore gestoßen. Diese gibt es in verschiedenen Traglasten
und erfüllen für mich (also den gelegentlichen Privatgebrauch) den gewünschten Zweck und sind dazu noch erstaunlich preiswert.
Ich habe mich für eine Schiene vom Typ RF55 mit 57x68mm Querschnitt und 300kg Nenntragfähigkeit entschieden. Laut Datenblatt
sollen die Haltewinkel in einem Abstand von 75cm angebracht werden. Jeder dieser Halter wird mit zwei Schrauben an der Decke
verankert.
In der Schiene läuft dann auf vier Kugellagern ein Rollenlaufwerk, welches an der Unterseite über eine M20er Gewinde verfügt.
Daran habe ich eine M20er Ringmutter geschraubt, welche dann den Haken eines Kettenzugs aufnimmt.
Für die Anbauteile der FP1 mit jeweils bis zu ca. 60kg ist das schon ziemlich überdimensioniert.
Aber besser so als wenn der Kran am Limit betrieben wird.
Um aber auch mal die komplette Maschine etwas verrücken zu können (die FP1 steht vor dem Fenster, welches sich jetzt nur noch
halb öffnen lässt), habe ich mich entschlossen alle 45cm (anatatt 75cm) einen der Haltewinkel mit zwei dicken Betonankern (Fischer FAZ II 10) zu fixieren.
Zudem habe ich zur besseren Lastverteilung an einem 40x60mm Vierkantrohr zwei Rollenlaufwerke in 45cm Abstand zueinander
befestigt. Mit dieser Konstruktion wird die Tragfähigkeit mehr als verdoppelt, weil die Last auf zwei Rollenlaufwerke und auch
(mindestens) zwei Deckenhalter verteilt wird.
Im Datenblatt des Herstellers ist eine Kurve angegeben die zeigt, dass die Schiene schon bei "normaler" Montage und nur
einem Rollenlaufwerk (also quasi Punktlast) 1500kg tragen kann, bevor ein Teil versagt. Da habe ich also mehr als genug Sicherheitsreserve!
Nicht vergessen: An beiden Enden der Kranbahn einen Endanschlag anbringen. Mit dem Originalteil des Herstellers verliert man an
jeder Seite fast 10cm der Nutzlänge. Ich habe stattdessen das Profil quer durchbohrt und jeweils eine M6er Schraube durchgesteckt
und gesichert. Das ist zwar kein weicher Anschlag, ich nutze die Konstruktion aber auch nicht als Schiebetor das man häufig bis
zum Anschlag öffnet und schließt.
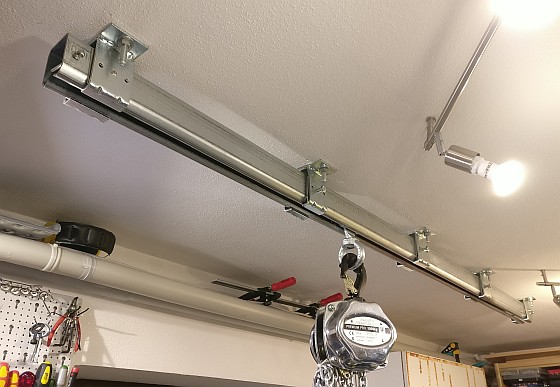
Bild 10 - Eine an die Decke geschraubte Laufschiene mit Rollenlaufwerk und Kettenzug dient als Kranbahn über der Fräsmaschine.
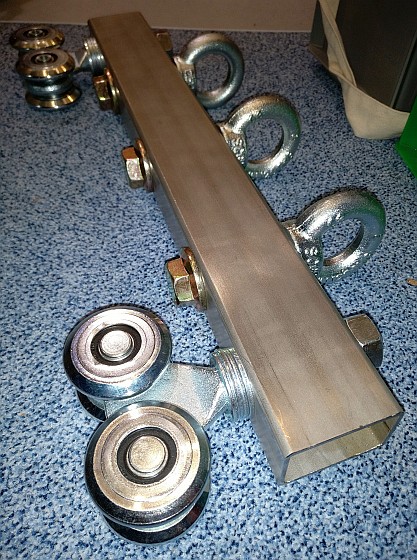
Bild 11 - Wenn mal die ganze Maschine an den Haken muss verwende ich diese Konstruktion welche die Last besser verteilt.
Manueller Kettenzug
Um am Rollenlaufwerk der Kranbahn auch etwas hochheben und auf einer Position fixieren zu können brauchte ich noch eine
Hebehilfe, die es erlaubt schwere Teile Millimetergenau in der Höhe zu positionieren.
Mit einem elektrischen Seilzug geht das nicht, der dreht viel zu schnell und arbeitet ruckartig.
Hierfür brauchte ich also etwas Mechanisches. Es kam ein Hebelzug oder ein Flaschenzug mit Steuerkette in Frage.
Beim Hebelzug befindet sich der Hebel naturgemäß oben am Gehäuse, ist also an einer sehr ungünstigen Position,
wenn man (ohne Helfer) weiter unten etwas ganz genau positionieren will. Hinzu kommt, dass beim Hebelzug
die Hebelbewegung auf das Gehäuse wirkt, so dass die Last unten sehr leicht ins schwingen gerät.
Beim Kettenzug bewegt man die Steuerkette dagegen nur ziehend nach unten, was dem schwingen der Last entgegen wirkt.
Auch ist diese Kette lang genug, um sie auf jeder beliebigen Höhe bedienen zu können.
Dafür ist sie gerne mal im Weg, weil sie knapp neben dem Lasthaken bis auf den Boden herunterhängt.
Ich habe mich für einen Planeta PremiumPro Kettenzug mit 1000kg Tragfähigkeit entschieden, weil der ausnahmsweise
günstiger zu bekommen war als die kleineren Ausführungen.
Die Untersetzung beträgt bei diesem 1:40, die Last lässt sich damit fast ohne Kraftanstrengung sehr exakt in der Höhe
justieren und wird auch an der gewünschten Position gehalten. Zum Lösen der automatischen Haltebremse muss man nur kurz
etwas fester ziehen.
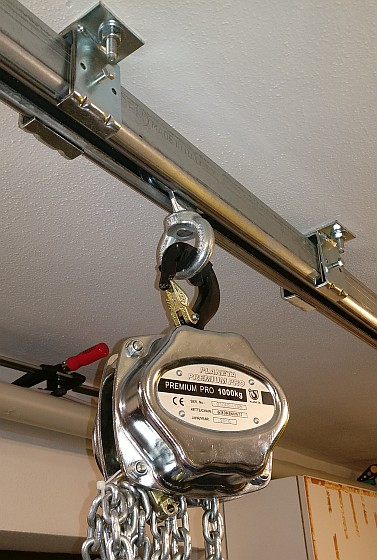
Bild 12 - Mit einem hochwertigem Kettenzug lässt sich die Last ruckfrei und millimetergenau positionieren.
Rundschlingen
Die wenigsten Teile haben eine Öse oder einen anderen direkten Anschlagpunkt für den Kranhaken.
Rundschlingen oder Hebebänder sind dann das Mittel der Wahl.
Diese gibt es in unterschiedlichsten Stärken und Längen, beginnend mit WLL 1000, also 1000kg.
Aber schon diese "leichten" Hebebänder sind relativ dick und starr. Die Teile der Fräsmaschine damit
sicher und eng zu umschlingen war teilweise schwierig bis fragwürdig. Schließlich darf das Band nicht
abrutschen können aber es darf auch keine Bedienteile der Last quetschen und beschädigen.
Aus diesem Grund habe ich mir aus dem Klettersportzubehör 16mm Bandschlingen (Expressschlingen ohne Karabiner)
besorgt. Das sind im Grunde auch Rundschlingen, nur sind sie sehr viel schlanker als die für reine Hebezwecke
vorgesehenen Bänder. Die Bruchlast ist mit 22kN angegeben, für meinen Einsatzzweck also mehr aus ausreichend.
Für manche Teile habe ich zusätzlich Spanngurte eingesetzt, um die Hebeschlingen sicher an Ort und Stelle
zu fixieren.
Ein Teil wie die Nutenplatte des Frästischs lässt sich überhaupt nicht mit Schlingen packen. Hierfür habe ich
zwei Nutsteine (12mm/M10) mit Ringschrauben (M10) in den Nuten des Tischs befestigt, siehe Bild 6 oben.
Bild 13 & 14 - Rundschlingen WLL1000 und Bandschlingen aus dem Klettersport zum anheben der Last
Holzbalken, Möbelroller, Schuhwerk etc.
Wenn man mit schwerem Gerät hantiert, muss man auch auf die eigene Sicherheit achten.
Fällt einem ein 50kg schwerer Frästisch auf den Fuß, dann sind bestimmt einige Knochen zertrümmert, aber
man kann sich (vermutlich) noch selber aus dieser Lage befreien und wirds wahrscheinlich auch überleben.
Wird dagegen ein Körperteil unter einem 200kg schweren Teil wie der Frässäule "begraben", hat man
ohne fremde Hilfe kaum eine Chance da raus zu kommen.
So oder so: So weit darf es nicht kommen!
Sicherheitsschuhe mit Stahlkappe sind für solche Arbeiten nicht verkehrt, auch wenn diese nur "kleine"
Ausrutscher vollständig abhalten kann.
Auch hat es sich als sinnvoll erwiesen immer ein paar Holzbalken (ca. 80x80mm oder mehr) parat zu haben, die
man beim heben und umlagern vorsorglich unterlegt. Reißt tatsächlich mal ein Seil oder eine Kette, dann
retten ein (oder besser zwei) solcher Balken zuverlässig den daneben stehenden Fuß.
Für den Transport der mittelschweren Anbauteile (Motor, Tisch etc.) auf ebenem Grund haben sich Möbelroller
als sehr praktisch erwiesen.
Bild 15 & 16 - Auf dem Rollbrett festgezurrt folgen einem die Teile wie ein Hündchen an der Leine :-)
Noch ein Hinweis zur Sicherheit:
Steht eine FP1 (oder einer der unzählichen Nachbauten anderer Hersteller) mit Maschinenfüßen mittig auf einer
Palette, dann ist die komplette Last nur auf den zwei Längsbrettern, welche gerade nicht von Klötzen unterstützt sind.
Diese Bretter biegen sich unter der Last auch kräftig durch. Das führt bei den Demontagearbeiten mit Ratsche und Hebel
zum Schaukeln der ganzen Maschine. Würde nun eines der Bretter brechen (man bekommt die schwersten Teile schließlich
grundsätzlich auf den abgewracktesten Paletten...), gerät der Schwerpunkt der Maschine so weit nach außen,
dass sie umkippen würde. Darum habe ich wann immer es möglich war zwei Kanthölzer quer durch
die ganze Palette geschoben, welche ein absacken der Füße beim Bruch eines der Bretter gestoppt hätten.
Wenn möglich erst eine OSB-Platte oder ähnliches zur Lastverteilung auf die Palette legen
und dann erst die Maschine draufstellen!
Werkzeuge
Wer darüber nachdenkt sich eine Industriefräsmaschine anzuschaffen wird vermutlich schon
über einen Grundstock an Werkzeugen verfügen.
Damit die (De-)Montage nicht immer wieder an fehlendem Werkzeug stockt, habe ich eine
Auflistung an nötigen und empfehlenswerten Werkzeugen. Diese Liste gilt natürlich nur für
eine FP1 meines Jahrgangs, neuere Maschinen sind möglicherweise im Detail etwas
anders aufgebaut und es wird anderes Werkzeug benötigt.
Knarrenkasten 1/4" und 1/2" und falls nicht dabei
1/2" Nüsse in 30mm und 32mm sowie
1/2" Verlängerung 50mm (40-65mm ist OK; notwendig für die M20 Schrauben in der Säule, hier geht es eng zu)
Gabel- und Ringschlüsselsatz 6-32mm
2 Stück Hakenschlüssel 40/42mm für die Muttern an der X-Spindel. Den Hersteller AMF kann ich empfehlen, billigere
gehen häufig schon bei der ersten Benutzung kaputt.
Splinttreiber 3, 4, 5 und 6mm
Schonhammer und einen schweren Gummihammer
Hochwertige Schlitzschraubendreher in allen gängigen Größen
Inbusschlüssel 3-10mm
Bitzsatz Schlitzschrauben und Inbus mit Adapter für die Ratsche
Ein Hinweis zum lösen fest sitzender Schrauben:
Bei Maschinen dieses Alters sind viele Schrauben einfache Schlitzschrauben. Durch Rost oder
unsaubere (Über-)Lackierung sitzen diese oft extrem fest. Aber gerde bei Schlitzschrauben
ist die Gefahr dass man abrutscht und dabei den Schraubenkopf beschädigt extrem groß.
Mit jedem Fehlversuch wird es dann schwieriger, weil der Schraubendreher in einem
vermackten Schraubenkopf erst recht keinen Halt mehr findet.
Um sich Ärger zu ersparen habe ich mir bei der FP1 folgendes angewöhnt:
Schlitz der Schraube komplett von Schmutz und Farbe freikratzen.
Exakt passenden Schraubendreher wählen, er sollte kein Spiel haben.
Schraubendreher mit einem kräftigen Schlag mit dem Schonhammer reintreiben.
Eine Hand drückt den Schraubendreher fest rein und mit der anderen dreht man ruckartig auf.
Bei Schraubendrehern mit einem Sechskant am Schaft kann man mit einem Gabelschlüssel mehr Drehmoment aufbringen
Wenn die Kraft zum Lösen immer noch nicht reicht, passendes Bit mit der Ratsche verwenden.
Nach der ersten Vierteldrehung sind die meisten Schrauben dann unproblematisch.
Weiter gehts zu Teil 3...
oder
Zurück zu Teil 1...
+
R. Emling, Juli 2019